Decking Edit window
( Modeling > F2 > "
Misc steel " > " Decking ")
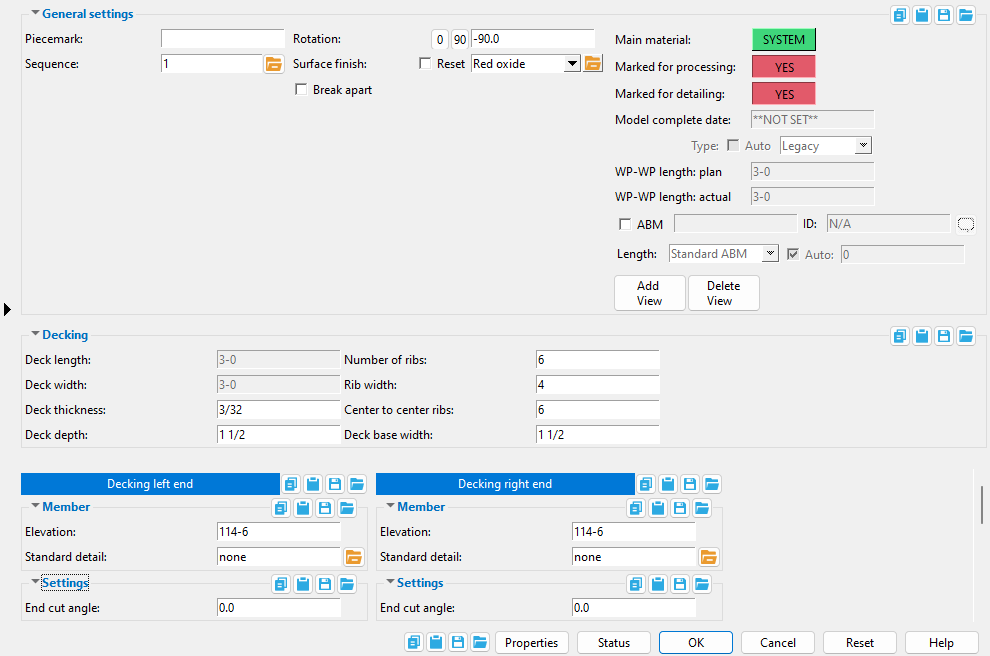
Selecting " Decking " as the " Miscellaneous steel " type adds a custom member with deck material to a 3D model.
This Decking custom member is a superior alternative to " Miscellaneous -- Decking ."
The edit window of this member features material and member options on the same window.
Its " General settings " include " Break apart " and " Rotation " which are not available for the legacy miscellaneous member.
Member operations such as many of those found on the Model > Member menu in Modeling can be performed on this member, and you can add custom components to it.
![]()
![]()
The " OK " button is disabled (grayed out) to indicate a validation error. Hover the " OK " button with your mouse pointer to get a listing of settings you need to change on this window. When all settings are valid, the " OK " button is enabled. ![]()
![]()
Red-colored highlighting identifies an entry that is invalid. You need to change that setting, or you will not be able to close this window using " OK ."
Also see:
- Material Types (topic)
- Miscellaneous member types (the complete list)
- Custom members (a decking miscellaneous member is a custom member)
- Deck Material (window can set Decking Edit 's " Main Material " to ' USER ')
- Miscellaneous members versus legacy miscellaneous members (topic)
- Surfaces Connection (a custom component you can add to a miscellaneous member)
1 . A decking miscellaneous member can be properly located and rotated even in an isometric view. Before adding the member, be aware of the following:
2 . To add a decking miscellaneous member (in Modeling ):
Alternative 1 : Press F2 > check the box for "
Miscellaneous steel " > double-click " Decking ."
Alternative 2 : Choose Model > Member > Prompt for Member Type > check the box for "
Miscellaneous steel " > double-click " Decking ."
3 . Locate - Repeat - Return mouse bindings become active, and you are prompted to locate the decking member's work points. Two work points are required to lay out decking.
![]() |
![]() |
bindings |
3a : Select the appropriate Locate option.
3b : Left-click ( Locate ) at two different on-screen positions to define the member line between those two points. The first work point you enter when you add the decking defines the left end of the member. Both points are represented as exact points after step 4, when the member is actually generated in the model.
![]()
![]()
The first point that you locate is identified by an origin symbol . The origin symbol also tells you which end is the member's left end. The following illustration shows the difference between locating the two points from left to right versus right to left
![]()
If you Model > Member > Isolate > ... a decking miscellaneous member, you will find that the member's MAIN VIEW shows the member's origin symbol (
) to be to your left. This is true for any miscellaneous member -- even if the origin symbol for the member is to your right in a plan view. The MAIN VIEW in member isolation directly correlates to the main view of the miscellaneous member's detail.
Best practice when adding a miscellaneous member in a plan view is to input the member from left to right or from bottom to top. That way, when you add a grid line from left to right, the near side of the member, as determined by the location of its left end , will be the side looking toward the bottom or toward the right of the screen.
4 . The Decking Edit window opens. On it are the settings for the deck you are adding.
4a : Be sure to make correct entries to the fields for " Deck thickness ," " Deck depth ," " Number of ribs ," " Rib width ," " Center to Center ribs " and " Deck base width ."
4b : Change the " Rotation " of the decking if you want it rotated. By default, decking is placed at a " Rotation " of ' -90 ', so that its ribs face toward you, out of the screen.
4c : Press the " OK " button at the bottom of the window to apply your settings and close the window.
Note: The default settings on this window are those of the last decking miscellaneous member added or edited in this session of Modeling . Even if all you do is double-click a decking member and press " OK " on its edit window, its settings become the defaults for the next-added decking miscellaneous member. You therefore only need to make changes to those settings which are different for this member.
5 . If User and Site Options > Modeling > " Automatically process after modeling operation " is ' Process and create solids ', the new decking will have automatically undergone all phases of Process and Create Solids and will show up in a solid form . If that option is ' Process ' or ' Do nothing ', then the member line of the decking you just added shows up on screen in stick form , and you will have to Process > Process and Create Solids in order to have the member piecemarked and able to be displayed in a solid form. Do one (1) of the following:
![]() |
![]() |
bindings |
Alternative 1 : Move the mouse pointer (
) and middle-click ( Repeat ) to lay out decking just like the last one beginning at the point where the point location target (
) is at. The X, Y global axes location of the repeated decking will begin from the located repeat point (where the target is at). The plate's Z location and other settings will be that of the last-added or last-edited decking.
Alternative 2 : Follow these instructions beginning with step 3 to add decking with different settings than the one you just laid out.
Alternative 3 : Right-click ( Return ) if you are done adding decking.
------ Decking ------
Decking length: read-only . The distance (in the primary dimension " Units " or other units ) spanned by the deck's member line.
The following can be used to track the choice made here when " Main material " is ' SYSTEM ':
Report Writer: XXXXX . Length
Advanced Selection: Length
Parametric module: Length
Deck width: read-only . This tells you the width (in the primary dimension " Units ") of the deck.
Note: Deck width is calculated using this formula: deck width = ( number of ribs )( C to C ribs ). This means that if you change the " Number of ribs " or " C to C ribs ," the deck width is recalculated.
The following can track the choice made here when " Main material " is ' SYSTEM ':
Report Writer: XXXXX . Width
Advanced Selection: Width
Parametric module: Width
Deck thickness: The thickness of the steel deck member (in the primary dimension " Units " or other units or the gage ).
To enter gage plate: Type in the ' gage number' followed by ' ga ' (example: ' 4ga ' is rewritten as ' 4GA ' when you Tab out of the field). Right-click tells you the stored thickness (based on industry standards), from which the weight of the gage plate is calculated. Allowable gages are any whole number from 3 to 38 . You can also enter an exact decimal thickness to get the gage (example: ' .1345 ' becomes ' 10GA ' when you Tab out of the field).
The following can read the choice made here when " Main material " is ' SYSTEM ':
Report Writer: XXXXX . Thickness
Advanced Selection: Thickness
Parametric module: Thickness
Deck depth: The distance (in the primary dimension " Units " or other units ) measured perpendicular to the member line of the deck from the bottom of the deck to the top of any one rib. In other words, this is the rib height.
![]() |
The bottom of the deck is at the elevation of its member line. |
The following can reveal the choice made here when " Main material " is ' SYSTEM ':
Report Writer: XXXXX . RibDepth
Advanced Selection: RibDepth
Parametric module: RibDepth
Number of ribs: The total quantity of ribs ( 1 or 2 or 3 or ...). Changing the number of ribs causes the " Decking width " to be recalculated.
![]() |
This deck was added in a plan view . Its ribs are the surfaces at the highest elevation. Each rib is as long as the " Decking length " is long. |
The following can be used to track the choice made here when " Main material " is ' SYSTEM ':
Report Writer: XXXXX . NumberOfRibs
Advanced Selection: NumberOfRibs
Parametric module: NumberOfRibs
Rib width: The width (in the primary dimension " Units " or other units ) of the top surface of any one rib. All ribs will be this same width.
Note: Changing the width of the ribs causes the " Decking width " to be recalculated.
The following can be used to show the choice made here when " Main material " is ' SYSTEM ':
Report Writer: XXXXX . RibWidth
Advanced Selection: RibWidth
Parametric module: RibWidth
Center to center ribs: The distance (in the primary dimension " Units " or other units ) from the center of any one rib to the center of an adjacent rib.
The following can track the choice made here when " Main material " is ' SYSTEM ':
Report Writer: XXXXX . RibSpacingCenterToCenter
Advanced Selection: RibSpacingCenterToCenter
Parametric module: RibSpacingCenterToCenter
Deck base width: The distance (in the primary dimension " Units " or other units ) from the inside corner of one bend to the inside corner of the next bend at the base of the deck.
![]() |
This deck's base width is less than the center-to-center spacing between ribs minus the rib width. |
![]() |
This deck's base width is the same as the center-to-center spacing between ribs minus the rib width. |
![]() |
This deck's base width is larger than the center-to-center spacing between ribs minus the rib width. |
The following can read the choice made here when " Main material " is ' SYSTEM ':
Report Writer: XXXXX . BaseWidth
Advanced Selection: BaseWidth
Parametric module: BaseWidth
|
|
|
------ Member ------
End elevation: The elevation (in the primary dimension " Units " or other units ) of the work point at this end of the decking. For non-sloping decking, both the left and right end elevations are the same. When you add the decking, its work points are placed in your current view's reference elevation until you change their elevations here, on this window.
Decking has four exact points . You can choose the elevation of the two along its member line by changing the member's left- and/or right-end " End elevation ." |
![]() |
To determine the end elevation on decking in the 3D model , use Construction Line Add or a similar tool, select EXPT as the Locate option, then snap the point location target to the work point at the end of the member. The Z coordinate reported in the X-Y-Z display tells you the elevation at the snapped-to exact point.
Tip: You should use this option instead of rotating a decking member's material to change its left- or right-end elevation. For complex situations, you can Model > Member > Move/Stretch one or the other of its work points.
Standard detail: None or a standard detail name . To apply a standard detail, you can type in the file name of the drawing (if you know it), or press the "file cabinet" browse button ( ) and double-click any job standard detail or global standard detail that is on the list.
If ' none ' is entered here, then no standard detail will be applied on this end of the miscellaneous member when it is automatically detailed .
If a ' standard detail name ' is entered here, the next time you auto detail this miscellaneous member, the reference point of the standard detail will align with the input work point on this end of the member, and the standard detail's bill of material will be combined with the member's bill of material. The detail is placed on a layer that is named after the standard detail plus a "_L" or "_R" suffix.
------ Settings ------
End cut angle: Any angle from 89 to -89 degrees. The cut will be made along the width of the decking.
For example, if the left end of the decking is to your left on your computer screen and negative distances along its Y member axis are toward the bottom of the screen: ' 0 ' (zero) square cuts the end. A ' positive angle ' is measured counterclockwise from a perpendicular bisector to the member line. A ' negative (-) angle ' is measured clockwise from a perpendicular bisector to the member line.
The following can be used to track the choice made here when " Main material " is ' SYSTEM ':
Report Writer: XXXXX . LeftEndCutAngle
Report Writer: XXXXX . RightEndCutAngle
Advanced Selection: EndCutAngle[0] or EndCutAngle[1]
Parametric module: EndCutAngle[0] or EndCutAngle[1]