Add Beam Stiffeners at Beam ( Modeling )
Tool summary :
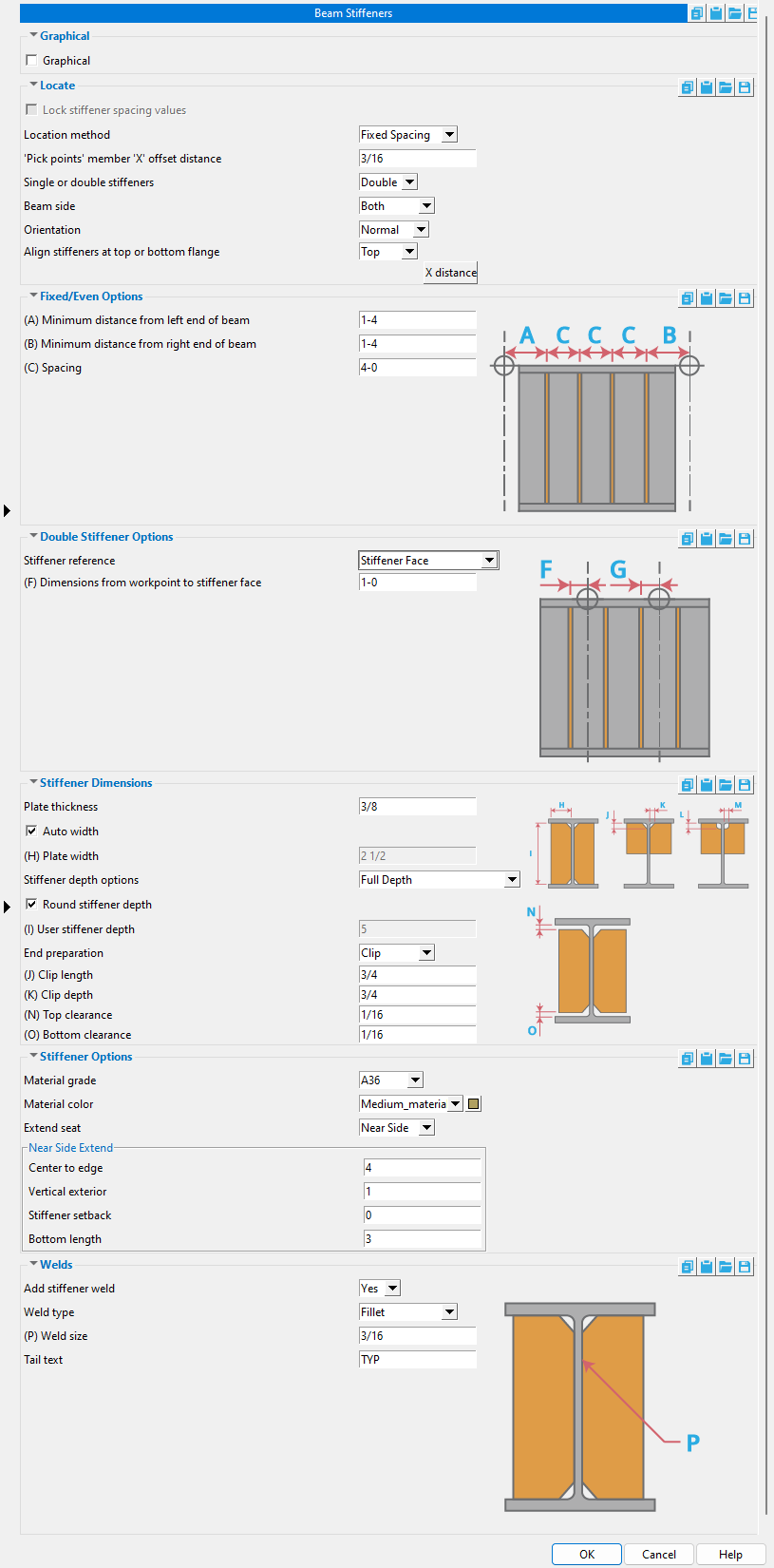
-
Location Method: Fixed Spacing
-
Orientation: Normal
-
Stiffener reference: Stiffener Face
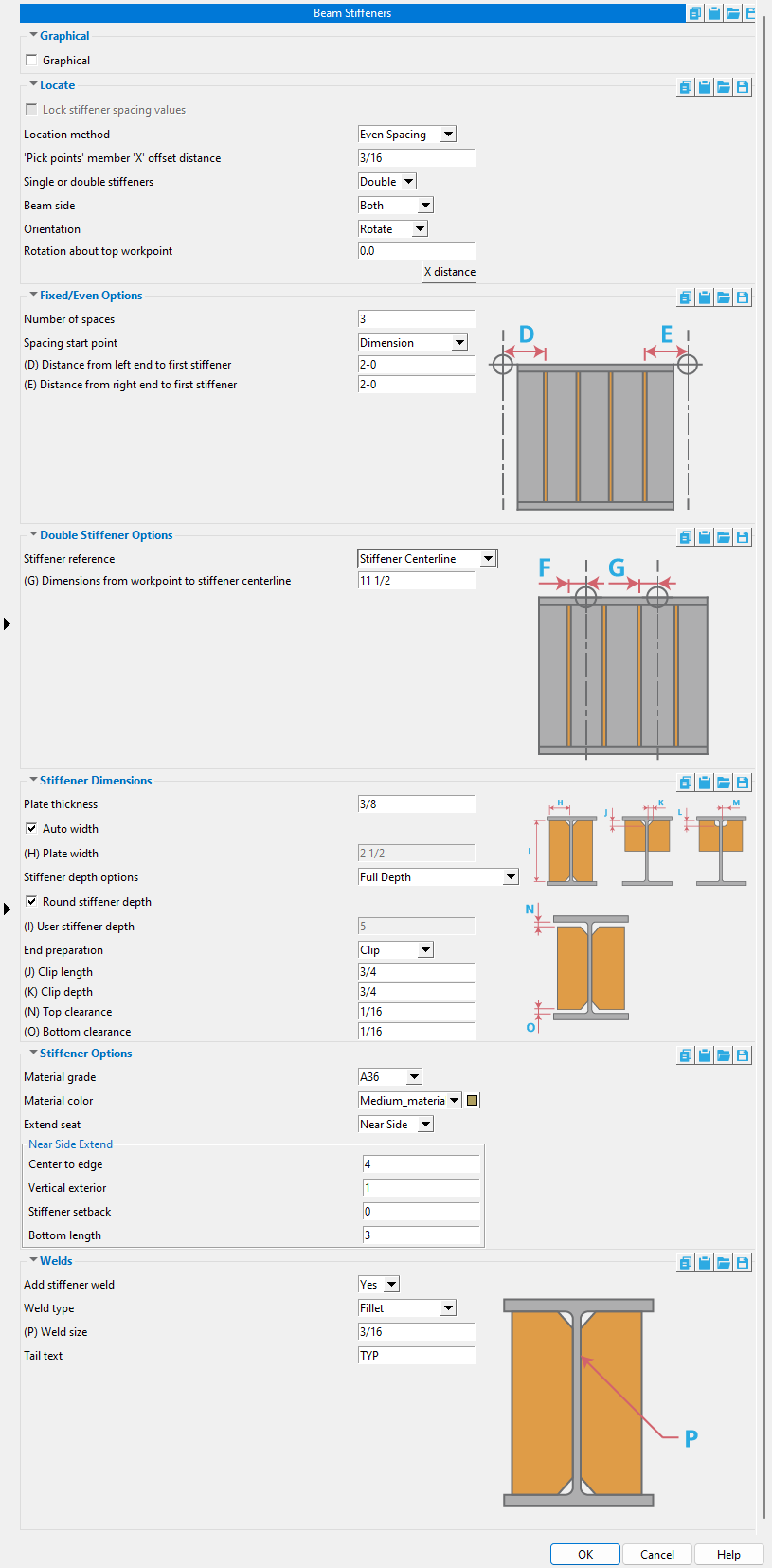
-
Location Method: Even Spacing
-
Orientation: Rotate
-
Stiffener reference: Stiffener Centerline
Also see :
- Modeling (where custom components can be added)
- Custom components (topic)
- Customers' Classroom: SDS2 Components 101 (YouTube) (
)
- Component Plugin Setup ( Home > Project Settings > Job )
- Copy Component (to copy the stiffeners to another beam)
- Move Component (to move the stiffeners to another beam)
- Explode Component (to reduce the component to its constituent materials and welds)
- Component Selection Tool (to search for custom components of a selected type)
- Model Tree (to find custom components and select them for deletion, editing, etc.)
page 1 | contents | add component | model > component (classic) | top
To add, edit or delete the Beam Stiffeners - Beam custom component :
![]()
Selecting any material or weld that is part of a custom component selects the entire component when the " Selection filter " is set to ' Default ' or ' All ' or ' Custom Components '',
page 1 | contents | add component | model > component (classic) | top
Beam Stiffeners - Beam custom component settings :
Graphical --------------------------------------------------------------------------------
Graphical : or
.
|
page 1 | contents | add component | model > component (classic) | top
Locate ------------------------------------------------------------------------------------
Lock stiffener spacing values: or
.
|
![]() |
" ![]() |
If this box is checked (
), the " X distance " values that are specified for the spacing of stiffeners will be locked, and you cannot manually change them. The locked values will continue to be displayed, but they will be grayed out (disabled).
If the box is not checked (
), the " X distance " values that are shown can be manually changes since they will be enabled (not grayed out).
Location method: Pick Points or Fixed Spacing or Even Spacing .
' Pick Points ' lets you select the points along the beam member line where you want the stiffeners. You need to be in an appropriate view. A plan view at the beam's left and right " End elevation " works well for a non-sloping beam. For a sloping beam, you should Snap to Surface on the beam's top flange. You may also want to lay out construction lines so that there are INCL or INCM points where you want to locate the stiffeners. Preparation for locating the points should be done before invoking Add Component . See " Pick points' member 'X' offset distance ."
' Fixed Spacing ' gives you options for setting the " Minimum distance from left end of beam " to the leftmost stiffener, and the " Minimum distance from right end of beam " to the rightmost stiffener. The " Spacing " between the stiffeners is fixed at the user-entered distance. A maximum number of stiffeners will be generated (at the fixed spacing) to fill the available space.
' Even Spacing ' results in automatic spacing that is evenly distributed between the " Number of spaces " you enter. The spacing will be across the beam's " WP to WP length, actual " when ' Workpoint ' is selected as the " Spacing start point ." It will be spaced across the length of the beam main material when ' Minus Dimension ' is selected as the " Spacing start point ."
'Pick points' member 'X' offset distance: A positive (+) or negative (-) distance (in the primary dimension " Units " or other units ). This applies when the " Location method " is ' Pick Points '. The offset adjusts the stiffeners' placement with respect to the points that you locate. Workpoints should be located along the beam's member line. The member line of a beam runs across its top flange.
![]() |
After you press " OK " on the Beam Stiffeners - Beam window, the status line will prompt you to locate points. The view shown here and below is the beam's top flange. |
![]() |
Process and Create Solids generates the stiffeners at the points that you located. For this example, an offset of half the stiffener thickness was applied. |
' 0 ' as the offset centers the stiffeners with respect to their thickness.
' a positive (+) distance ' offsets the placement of the stiffeners to the right of the point located. The amount of offset is the distance entered. For example, entering an offset distance of half the thickness of the stiffeners locates those stiffeners at their left-facing face instead of their center line.
' a negative (-) distance ' offsets the placement of the stiffeners to the right of the point located. The amount of offset is the distance entered.
Single or double stiffeners: Single or Double .
' Single ' places a single stiffener (or a pair of near-side and far-side stiffeners) at the spacing that is based on the " Location method " that is selected.
' Double ' places twice as many stiffeners, evenly spaced between the spacing that is set per the selected " Location method ." See " Double stiffener options ."
Beam side: Near Side or Both or Far Side .
![]() |
![]() |
![]() |
The left end of the beam is shown in all three of these examples.
|
' Near Side ' places the stiffeners on the near side of the beam. If you are looking at the web of a beam, and the left end of the beam is to your left, then you are looking at the near side web of the beam.
' Both ' places the stiffeners on both the near side and far side of the beam.
' Far Side ' places the stiffeners on the far side of the beam's web.
Orientation: Normal or Vertical or Rotate .
' Normal ' orients the stiffeners normal to the beam. That is, the stiffeners will be perpendicular to the beam's flanges.
' Vertical ' orients the stiffeners vertically.
' Rotate ' lets you, the user, specify the rotation of the stiffeners by entering a number of degrees for the " Rotation about top workpoint . "
Align stiffeners at top or bottom flange: Top or Bottom . This applies when the " Orientation " is set to ' Normal '.
Rotation about top workpoint: A positive (+) or negative (-) number of degrees . This rotation can be applied when the " Orientation " is set to ' Rotate '.
' 0 ' degrees positions the stiffeners normal to the beam.
A positive number of degrees rotates the stiffeners clockwise around the top workpoint when you are looking at the near side of the beam.
A negative number of degrees rotates the stiffeners counterclockwise around the top workpoint when you are looking at the near side of the beam.
X distance: A table that is filled out after the Beam Stiffeners - Beam custom component undergoes Process and Create Solids . The table tells you the positioning points of the stiffeners from the left end workpoint of the beam. The values reported in the table are editable, but you must check the box for " Lock stiffener spacing values " if you want to keep Process and Create Solids from changing the values.
![]() |
The " X distance " reported for a stiffener positioning point is from the workpoint of the beam -- even when the " Spacing start point " is set to ' Minus dimension '. Also, the " X distance " locates the centerline of the stiffener when ' Single ' is selected. It locates a midpoint between ' Double ' stiffeners. |
|
page 1 | contents | add component | model > component (classic) | top
Fixed/Even Options ------------------------------------------------------------------
Minimum distance from left end of beam: A distance (in the primary dimension " Units " or other units ). This applies when the " Location method " is ' Fixed Spacing '. The stiffener that is nearest to the left end of the beam will be placed at least this distance away from the left-end workpoint of the beam. The " Minimum distance ... " is measured to the centerline of the stiffener.
![]() |
There is no minus dimension setback on the 5-foot beam that is shown in this example. Since the " Minimum distance from left end of beam " is ' 8 ' inches, .the leftmost stiffener is placed 8 inches or farther away from the left end workpoint. In this example, it is placed 1 foot away from the left end workpoint. The distance of 1 foot makes room for two spaces at a " Spacing " of 1'-6" with 1 foot left over for the distance from the centerline of the last stiffener to the right end workpoint. |
Minimum distance from right end of beam: A distance (in the primary dimension " Units " or other units ). This applies when the " Location method " is ' Fixed Spacing '. The stiffener that is nearest to the right end of the beam will be at least this distance away from the right-end workpoint of the beam.
![]() |
On this 5-foot beam with no minus dimension setback, the rightmost stiffener is placed 1 foot away from the right end of the member's main material. One foot is greater than ' 8 ' inches, which is the " Minimum distance from right end of beam " in this example. |
Spacing: A distance (in the primary dimension " Units " or other units ). This spacing applies when the " Location method " is ' Fixed Spacing '. The spacing is measured from the centerline of one stiffener to the next. The stiffeners will be "fixed" at this distance apart from another unless " Lock stiffener spacing values " is checked.
![]() |
A 5-0 foot beam with no minus dimension setback. Since the " Minimum distance ... " for each end is ' 8 ' inches, that leaves a maximum of 3'-8" of available space for the stiffeners. Since the stiffeners are set to have a " Spacing " of 1'-6", three stiffeners (with two 1'-6" spaces between them) are able to fill the available space. |
Number of spaces: The number (a count) of spaces. This applies when the " Location method " is ' Even Spacing '. The spaces are counted differently if the " Spacing start point " is ' Workpoint ' or ' Minus dimension ' as opposed to ' Dimension '.
If " Spacing start point " is ' Workpoint ' or ' Minus Dimension ', this count is the spacing between stiffeners plus 2. The 2 added spaces are: 1 ) The space from the left end of the beam to the leftmost stiffener. 2 ) The space from the right end of the beam to the rightmost stiffener.
If " Spacing start point " is ' Dimension ', this count is the spacing between stiffeners only. The count does not include the distances from the ends of the beam to the outermost stiffeners since those values are defined by the " Distance from left end to first stiffener " and " Distance from right end to first stiffener ."
Spacing start point: Workpoint or Minus Dimension or Dimension . The starting point when the " Location method " is ' Even Spacing '.
'Workpoint' or 'Minus Dimension' defines where the space from the end of the beam to the nearest stiffener is measured from. If ' Workpoint ' is selected, the two outermost spaces are measured from the left/right workpoint to the nearest stiffener. If ' Minus Dimension ' is selected, the two outermost spaces are measured from the left/right end of the main material to the nearest stiffener.
![]() |
![]() |
' Dimension ' gives you options for " Distance from left end to first stiffener " and " Distance from right end to first stiffener ," which are measured from the left and right end workpoints of the beam.
Distance from left end to first stiffener
and
Distance from right end to first stiffener: A distance (in the primary dimension " Units " or other units ) from the left/right beam workpoint to the stiffener that is nearest to that end. These settings apply when " Spacing starting point " is set to ' Dimension '.
![]()
In this example of ' Even Spacing ', the " Number of spaces " is ' 3 ' and the " Spacing start point " is set to ' Dimension '. Each space is automatically calculated to evenly fill up the available space between the user-entered dimensions from the left/right ends ( lft and rt ). The automatically calculated even spacing between stiffeners is represented in this example as the value x.
page 1 | contents | add component | model > component (classic) | top
Double Stiffener Options -----------------------------------------------------------
Stiffener reference: Stiffener Face or Stiffener Centerline . This applies when ' Double ' stiffeners are selected.
' Stiffener Face ' gives you an option to " Dimension from workpoint to stiffener face ."
' Stiffener Centerline ' gives you an option to " Dimension from workpoint to stiffener centerline ."
Dimension from workpoint to stiffener face: The distance (in the primary dimension " Units " or other units ) from each " X distance " location to the nearest face of each of the two stiffeners (the ' Double ' stiffeners). This applies when " Stiffener reference " is set to ' Stiffener Face ," which applies when ' Double ' stiffeners are selected.
Dimension from workpoint to stiffener centerline: The distance (in the primary dimension " Units " or other units ) from each " X distance " location to the centerline of each of the two stiffeners (the ' Double ' stiffeners). This applies when " Stiffener reference " is set to ' Stiffener Centerline ," which applies when ' Double ' stiffeners are selected.
page 1 | contents | add component | model > component (classic) | top
Stiffener Dimensions ---------------------------------------------------------------
Plate thickness: A distance (in the primary dimension " Units " or other units ). This distance will be The " Material thickness " of the rectangular plate material that the beam stiffeners are made of.
![]() |
The calculated auto width of the stiffener sets the " Material width " of the rectangular plate that the stiffener is made from. |
If this box is checked (
), the width of each stiffener is based on the flange width (bf) of the beam. A clearance that is approximately equal to the beam web thickness (tw) is placed between the edge of the plate and the edge of the flange.
If the box is not checked (
), the width of each stiffener is the " Plate width " that is entered below.
Plate width: A distance (in the primary dimension " Units " or other units ). This applies when " Auto width " is not checked.
![]() |
The " Plate width " entered here is made the " Material width " of the stiffener when " ![]() |
Stiffener depth options: Full Depth or Top Flange Half Depth or Bottom Flange Half Depth or Top Flange Bottom K or Bottom Flange Top K or Top Flange User Depth or Bottom Flange User Depth . The stiffeners will be sized automatically based on the " Depth " specified for the beam's section size in the local shape file .
![]()
' Full Depth ' extends each stiffener to the inside surfaces of the top and bottom flanges of the beam.
' Top Flange Half Depth ' extends the top edge of each stiffener to the inside surface of the top flange of the beam and the bottom edge of each stiffener to the half-depth of the beam.
' Bottom Flange Half Depth ' extends the bottom edge of each stiffener to the inside surface of the bottom flange of the beam and the top edge of each stiffener to the half-depth of the beam.
' Top Flange Bottom k ' extends the top edge of each stiffener to the inside surface of the top flange of the beam and the bottom edge of each stiffener to the k distance from the outside surface of the beam's bottom flange.
' Bottom Flange Top k ' extends the bottom edge of each stiffener to the inside surface of the bottom flange of the beam and the top edge of each stiffener to the k distance from the outside surface of the beam's top flange.
' Top Flange User Depth ' extends the top edge of each stiffener to the inside surface of the top flange of the beam and the bottom edge of each stiffener to the " User stiffener depth " from the stiffener's top edge.
' Bottom Flange User Depth ' extends the bottom edge of each stiffener to the inside surface of the bottom flange of the beam and the top edge of each stiffener to the " User stiffener depth " from the stiffener's bottom edge.
User stiffener depth: A distance (in the primary dimension " Units " or other units ). When " Stiffener depth options " is set to ' Top Flange User Depth ' or ' Bottom Flange User Depth ," the value that is entered here sets the depth of the stiffener plates. On the Rectangular Plate Material window, this will be the " Order length " of each of the plates.
End preparation: Clip or Cope or Exact Fit .
' Clip ' gives you options for entering a " Clip depth " and a " Clip length ." See the illustration above.
' Cope ' gives you options for entering a " Cope depth " and " Cope length ." See the illustration above.
' Exact Fit ' exactly cuts the plate to the profile of the beam with a 1/16 inch clearance.
Top clearance: The distance (in the primary dimension " Units " or other units ) from the top edge of each stiffener and the inside surface of the top flange of the beam.
Bottom clearance: The distance (in the primary dimension " Units " or other units ) from the bottom edge of each stiffener and the inside surface of the bottom flange of the beam.
page 1 | contents | add component | model > component (classic) | top
Stiffener Options ---------------------------------------------------------------------
Material grade: A36 or A572 or etc. This is the grade of steel for the stiffeners. This is also the " Steel grade " of the rectangular plate material that each stiffener is made of.
Setup: This list box (
) is populated by entries made at Home > Project Settings > Job > Plate Grades .
Material color: A predefined color or a custom color . This is the approximate color of the stiffener plates when the beam they are submaterials of is displayed in one of the three solid forms . This is also the " Color " of the rectangular plate material that a stiffener is made of.
The predefined colors are set up on the Predefined Colors window. The color swatch next to the list box (
) displays the color that is selected.
Select ' Custom Color ' (last choice on the list) to launch your operating system's color picker and define any color you like.
Extend seat: None or Near Side or Far Side or Both .
![]() |
These views show the left end of the beam. |
' None ' keeps the stiffeners unextended.
' Near Side ' adds an extend seat to the near side , top flange of the beam and extends the near side stiffeners to the seat based on the choices that you make to the options that become available. These options are " Center to edge ," " Vertical exterior ," " Stiffener Setback " and " Bottom length ."
' Far Side ' gives the same results as ' Near Side ', but for the stiffeners on the far side of the beam.
' Both ' adds extend seats to both the near side and far side of the beam and extends the stiffeners on those sides to them.
Center to edge: The distance (in the primary dimension " Units " or other units ) from the work line of the beam to the furthest edge of the extend seat. This distance must be greater than half the flange width (bf) of the beam. The " Material width " of the extend seat will be the " Center to edge " distance entered here minus half the flange width (bf) of the beam. The " Center to edge " option applies when " Extend seat " has been set to ' Near Side ' or ' Far Side ' or ' Both '.
Vertical exterior: A distance (in the primary dimension " Units " or other units ). This is the length of the outside vertical edge of the stiffener plate. The " Vertical exterior " option applies when " Extend seat " has been set to ' Near Side ' or ' Far Side ' or ' Both '.
Stiffener setback: The distance (in the primary dimension " Units " or other units ) that the outside edge of the stiffener plate is to be set back from the outside edge of the extend seat. If a distance of ' 0 ' is entered, the outside vertical edge of the stiffener plate will go all the way to the outside edge of the extend seat. The " Stiffener setback " option applies when " Extend seat " has been set to ' Near Side ' or ' Far Side ' or ' Both '.
Bottom length: The distance (in the primary dimension " Units " or other units ) of the bottom edge of the stiffener plate that is parallel to and welds to the inside face of the bottom flange of the beam. The " Bottom length " option applies when " Extend seat " has been set to ' Near Side ' or ' Far Side ' or ' Both '.
page 1 | contents | add component | model > component (classic) | top
Welds ----------------------------------------------------------------------------------
Add stiffener weld: Yes or No .
' Yes ' shop welds the stiffeners to the beam.
' No ' instructs the Beam Stiffeners - Beam custom component to not add welds.
Weld type: Fillet or Square groove or Bevel groove . This sets the " Weld type " on the Weld Edit window in Modeling as well as the " Weld type " for the weld symbol on the beam detail.
symbol | name | weld used for... |
![]() |
fillet | General welding of material. |
![]() |
square groove | Butt joints of material 3/8" thick or less. |
![]() |
bevel groove | General full penetration welding of material. |
Weld size: A distance (in the primary dimension " Units " or other units ) that indicates depth of preparation, size or strength of the weld. This sets the " Weld size " on the Weld Edit window in Modeling as well as the " Weld size " for the weld symbol on the beam detail.
Tail text: blank or a text string . This sets the " Supplementary tail text " on the Weld Edit window in Modeling as well as the " Supplementary tail text " for the weld symbol on the beam detail.
|
" TYP " is this weld symbol's tail text. |
If this field is left ' blank ', a tail is not drawn on the weld symbol.
If a ' string of characters ' is entered, a tail with that character string as the tail text is drawn on the weld symbol.
page 1 | contents | add component | model > component (classic) | top