Embed Plate
- General Overview
- Step-By-Step
- Tips and Tricks
- Related Tools
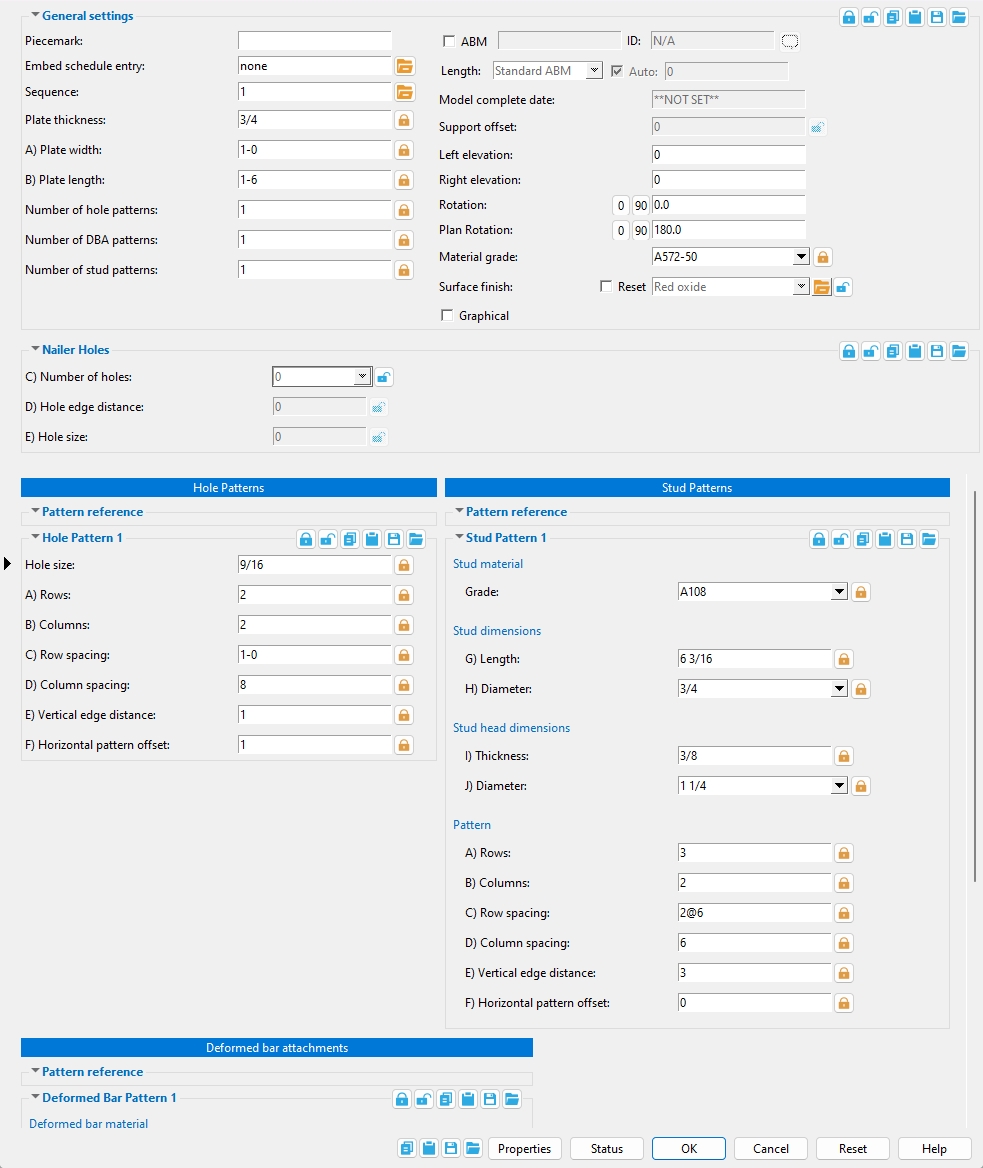
General Settings
Piecemark: Blank or a system piecemark or a user-entered string (of up to 61 characters ) which identifies this embed plate member as having an unique design distinct from other members that have been assigned different piecemarks. This is the member piecemark of the embed plate member.
Blank indicates that SDS2 piecemarking will assign a system piecemark to the embed plate member when you press OK to close this window. PIecemark is, by default, left blank when you first add a new embed plate.
A system piecemark ( system piecemark ) is the Piecemark that SDS2 piecemarking has assigned.
A user piecemark is a user-entered string. SDS2 piecemarking will not assign new members that user piecemark, nor will piecemarking remove that user piecemark from members to which it has been assigned. It is your responsibility to ensure that the same user piecemark is not used for another distinctly different member.
Tip: You can get rid of a user piecemark that has been assigned to an embed member by clearing the Piecemark entry and leaving the field blank. When you press OK, SDS2 piecemarking routines will automatically assign a system piecemark to the member.
Embed schedule entry: A standard piecemark name from the Piecemark column in the Embed Schedule. Only embed plate definitions or None are available for entry here if you are adding or editing an embed plate.
Sequence: Any sequence name from the Sequence Names setup list can be entered here.
To assign a different sequence, you can type in any sequence name that is on the Sequence Names list, or you can press the browse button and double-click any sequence name that is on the list.
Defaults: The sequence assigned by default to the first embed plate member that is added after you first start up Modeling is the sequence listed in line 1 of the Sequence Names list. For each embed plate member that you subsequently add during the same session in Modeling, the sequence that is assigned by default is the sequence assigned to the last-added or last-edited member.
Plate thickness: The thickness of the embed plate.
![]() |
t = plate thickness. |
If Plate thickness
is unlocked, the thickness shown here is the Plate thickness in Job > Connections > Embed Schedule that is entered for the selected Embed schedule entry.
If Plate thickness
is locked, you can enter a different thickness. The new thickness you enter will no longer match the corresponding entry made to the schedule. When you press OK and the SDS2 piecemarking evaluates your change, a new Piecemark may be assigned.
Plate width: The width of the embed plate. Plate width is a horizontal dimension when the Left elevation and Right elevation of the embed plate are the same. Since embed plates are rectangular, the top and bottom edges of an embed plate are each this same width.
If Plate width
is unlocked, the width shown here is the Plate width in Job > Connections > Embed Schedule that is entered for the selected Embed plate entry.
If Plate width
is locked, you can enter a different width. The new width you enter will no longer match the corresponding entry made to the schedule. When you press OK and the SDS2 piecemarking evaluates your change, a new Piecemark may be assigned.
Plate length: The length of the embed plate. Plate length is a vertical dimension. Since embed plates are rectangular, the vertical edges of an embed plate are each this same length.
If Plate length
is unlocked, the length shown here is the Plate length in Job > Connections > Embed Schedule that is entered for the selected Embed schedule entry.
If Plate length
is locked, you can enter a different length. The new length you enter will no longer match the corresponding entry made to the schedule. When you press OK and SDS2 piecemarking evaluates your change, a new Piecemark may be assigned.
Number of hole patterns: The quantity of hole patterns. To change the number, first set Number of hole patterns to locked.
0 results in there being no leaf for
Hole Pattern on this window.
1 or more results in one or more leaves on this window.
Job > Connections > Embed Schedule: Number of hole patterns.
Number of DBA patterns:The quantity of DBA patterns. To change the number, you can alter the Embed schedule entry, or you can change Number of deformed bar attachments to locked.
0 results in there being no leaf for
Deformed Bar Pattern on this window.
1 or more results in one or more leaves on this window.
Job > Connections > Embed Schedule: Number of DBA patterns.
Number of stud patterns: The quantity of Stud patterns. To change the number, you can alter the Embed schedule entry, or you can change Number of stud patterns to locked.
0 results in there being no leaf for
Stud Pattern on this window.
1 or more results in one or more leaves on this window.
Job > Connections > Embed Schedule: Number of stud patterns.
Model complete date: **NOT SET** or a month day year (see entering dates ).
**NOT SET** removes the designation of Model complete from this embed member, thus allowing the member to be physically altered. Type in 0 to enter **NOT SET** -- see entering dates.
If a month day year is entered, settings on this window are grayed out and cannot be changed. The affected embed member is prevented from being altered during the solids creation phase of Process and Create Solids.
Support offset: A positive or negative distance. This places the top of the embed plate the specified distance down or up from the top of a beam or joist
A positive distance moves the embed down from the top of the beam or joist.
A negative distance moves the embed up from the top of the beam or joist.
Left elevation: The elevation of the work point at the left end of the embed plate. The embed plate member line is set using the left elevation and right elevation.
Right elevation ( plate ): Same as Left elevation, except that this is the elevation of the right end of the embed plate.
Rotation: A positive or negative (-) number of degrees greater than -180° or less than or equal to 180°. This controls the rotation of an embed plate about the member line.
![]() |
An embed plate shown in an elevation view. The member line of the embed plate is horizontal. That is, both its Left elevation and Right elevation are the same. |
Plan rotation: A positive or negative (-) number of degrees greater than -180° or less than or equal to 180°. The left end of an embed plate member depends on its Plan rotation.
Plan Views | ||
Plan rotation is the same even when not attached to a beam. | ||
![]() |
![]() |
![]() |
-90 degrees orients the embed plate vertically in a plan view, with shear studs or DBAs pointed to the left. This is a good choice to make for an embed plate at the left end of a beam that is oriented horizontally in a plan view.
0 degrees orients the embed plate horizontally in a plan view, with shear studs or DBAs pointed down. This is a good choice to make for an embed plate at the left end of a beam that is oriented vertically in a plan view.
90 degrees orients the embed plate vertically in a plan view, with shear studs or DBAs pointed to the right. This is a good choice to make for an embed plate at the right end of a beam that is oriented horizontally in a plan view.
180 degrees orients the embed plate horizontally in a plan view, with shear studs or DBAs pointed up. This is a good choice to make for an embed plate at the right end of a beam that is oriented vertically in a plan view.
Material grade: A36 or A572 or etc. This is the Steel grade of the rectangular plate material.
If Material grade
is unlocked, the steel grade shown here is the Material grade in Job > Connections > Embed Schedule that is entered for the selected Embed schedule entry.
If Material grade
is locked, you can enter a different steel grade. That new grade will no longer match the corresponding entry made to the schedule. When you press OK and SDS2 piecemarking evaluates your change, a new Piecemark may be assigned.
Job > Connections > Embed Schedule: Material grade
Job Setup: If the grade of steel you want is not shown on the
list box, you can use Home > Project Settings > Job > Material Grades > Plate Grades to add it to the list.
Surface finish: None or Sandblasted or Red oxide or Yellow zinc or Gray oxide or Blued steel or Galvanized or Duplex Coating or Undefined 1 or Undefined 2 or Undefined 3 or Red oxide 2 or Any user added surface finish. This affects the colors of Solid members on erection views in the Drawing Editor. This also sets the color when Output material color is set to Surface finish for a VRML Export or a DWG/DXF Export. The Color (not Surface finish) sets the color of this material in Modeling.
sand blasted | red oxide | yellow zinc | user surface finish 1 |
gray oxide | blued steel | galvanized | user surface finish 2 |
Reset :
or
If this box
is checked, all attached materials' surface finish are reset to follow what is selected on the member level, with the check box checked on for auto inside of the material edit window, when the window is closed by selecting the OK button (or the Enter key).
If the box
is not checked, all attached materials' surface finish remains at what is set inside the material edit window.
Note 1: If the material surface finish changes from what the member level has set, an information tag is shown next to the surface finish in the member edit window. This notifies the user that an attached material has been changed by a user from what was set on the member level.
Note 2: Member Piecemarks can be split apart by surface finish. All surface finishes that do not have the Break Marks Member checked on can be applied to any like member with out the member splitting. If the Break Marks Member is checked on then only like members with that specific surface finish can have the same piecemark.
Graphical: or
If Graphical
is checked, then changes made on the embed's edit window will not be applied, thus preserving all graphical changes that were made to the embed member. This means that when you press OK on the edit window, or when you Process, no new materials will be generated.
If Graphical
is not checked, then changes made on the embed's edit window will be applied. Any graphical changes that you made to materials, bolts and welds will be lost.
Warning: Any graphical changes that you make to materials will be preserved only so long as the custom member is set to
Graphical. For this reason, you should make changes on a custom member's edit window before you begin to graphically alter the custom-member material. Otherwise, any graphical changes that you make will be lost.
Nailer Holes
|
0 results in no nailer holes.
2 results in two nailer holes, placed diagonally, at opposite corners of the embed plate.
4 results in four nailer holes, one at each corner of the embed plate.
Hole edge distance: The distance from the center of each nailer hole to the horizontal edge of the embed plate. This is also the distance of the nailer hole or vertical edge of the embed plate.
![]() |
ed = hole edge distance. |
If Hole edge distance
is unlocked, the distance shown here is the Hole edge distance in Job > Connections > Embed Schedule that is entered for the selected Embed schedule entry.
If Hole size
is locked, you can enter a different edge distance that no longer matches the corresponding entry made to the schedule. When you press OK and SDS2 piecemarking evaluates your change, a new Piecemark may be assigned.
Hole size: The diameter of the nailer holes. To change this setting without altering the schedule entry, Hole size must be locked.
If Hole size
is unlocked, the diameter shown here is the Hole size in Job > Connections > Embed Schedule that is entered for the selected Embed schedule entry.
If Hole size
is locked, you can enter a different diameter that no longer matches the corresponding entry made to the schedule. When you press OK and SDS2 piecemarking evaluates your change, a new Piecemark may be assigned.
Hole Patterns
Hole size: The diameter of the holes in this hole pattern.
If Hole size
is unlocked, the diameter shown here is the Hole size in Job > Connections > Embed Schedule that is entered for the selected Embed schedule entry.
If Hole size
is locked, you can enter a different diameter that no longer matches the corresponding entry made to the schedule. When you press OK and SDS2 piecemarking evaluates your change, a new Piecemark may be assigned.
Rows: The number of rows of holes. A single distance or variable spacing can be entered as the Row spacing for these rows.
![]() |
3 is the number of rows of holes in this example. |
If Rows
is unlocked, the count shown here is the Rows in Job > Connections > Embed Schedule that is entered for the selected Embed schedule entry.
If Rows
is locked, you can enter a different count that no longer matches the corresponding entry made to the schedule. When you press OK and SDS2 piecemarking evaluates your change, a new Piecemark may be assigned.
Columns: The number of columns of holes.
![]() |
2 is the number of columns of holes in this example. |
If Columns
is unlocked, the count shown here is the Columns in Job > Connections > Embed Schedule that is entered for the selected Embed schedule entry.
If Columns
is locked, you can enter a different count that no longer matches the corresponding entry made to the schedule. When you press OK and SDS2 piecemarking evaluates your change, a new Piecemark may be assigned.
Row spacing: A center-to-center distance or variable spacing. The distance between adjacent Rows of holes. This distance is measured vertically in the typical situation where the embed plate's Left elevation and Right elevation are the same.
![]() |
rsp = row spacing. |
Row spacing ( variable ) can be defined in a number of different ways, as the examples in the following table show.
Variable Hole Row Spacing | ||
Rows | Spacing | Result |
5 | 3,5,3,3 | 4 spaces at 3", 5", 3" and 3" |
5 | 3,5,2@3 | 4 spaces at 3", 5", 3" and 3" |
5 | 3,5,3 |
4 spaces at 3", 5", 3" and 3"
(Three spacings are entered, but four are required since the number of rows is 5. The last value is repeated to fill the fourth space.) |
If Row spacing
is unlocked, the distance shown here is the Row spacing in Job > Connections > Embed Schedule that is entered for the selected Embed schedule entry.
If Row spacing
is locked, you can enter a different distance that no longer matches the corresponding entry made to the schedule. When you press OK and SDS2 piecemarking evaluates your change, a new Piecemark may be assigned.
Column spacing: The distance between adjacent columns of holes. To change this distance, you can alter the Embed schedule entry, or you can set the Column spacing to locked.
![]() |
csp = column spacing. |
If Column spacing
is unlocked, the distance shown here is the Column spacing in Job > Connections > Embed Schedule that is entered for the selected Embed schedule entry.
If Column spacing
is locked, you can enter a different distance that no longer matches the corresponding entry made to the schedule. When you press OK and SDS2 piecemarking evaluates your change, a new Piecemark may be assigned.
Vertical edge distance: The distance from the top edge of the embed plate to the first row of holes. To change this distance, you can alter the Embed schedule entry, or you can set the Vertical edge distance to locked.
![]() |
ved = vertical edge distance. |
If Vertical edge distance
is unlocked, the distance shown here is the Vertical edge distance in Job > Connections > Embed Schedule that is entered for the selected Embed schedule entry.
If Vertical edge distance
is locked, you can enter a different distance that no longer matches the corresponding entry made to the schedule. When you press OK and SDS2 piecemarking evaluates your change, a new Piecemark may be assigned.
Horizontal pattern offset: A distance that the hole pattern is offset. To change the entry made here, Horizontal pattern offset needs to be locked.
![]() |
0 centers the hole pattern at the horizontal center of the embed plate, half way between the plate's vertical edges -- at the plate width center line.
A positive distance offsets the center of the hole pattern that distance away from the true horizontal center of the embed plate. The hole pattern is moved away from the origin point.
A negative distance does the opposite of entering a positive offset. The hole pattern is moved toward the origin point.
Deformed Bar attachments
Deformed bar material
Section size: Any round bar Section size that is maintained in the local shape file.
If Section size
is locked, you can type in the section size that you want, or you can press the browse button
and double-click a section size from the list that opens. The list includes only the section sizes that are in the local shape file. Validation will not let you enter a section size that does not exist in the local shape file.
Grade: Any steel grade that is available at Home > Project Settings > Job > Material Grades > Round and Square Bar Grades can be selected here.
If Grade
is locked, you can select a different steel grade that no longer matches the corresponding entry made to the schedule. When you press OK and SDS2 piecemarking evaluates your change, a new Piecemark may be assigned.
Length: The actual length when DBA when the End operation is None. For DBAs with an End operation of Hook, the actual unbent length of the DBA will be substantially larger than this Length. For DBAs with an End operation of Bend, the actual unbent length of the DBA will be a bit larger than this Length.
If Length
is locked, you can select a different length that no longer matches the corresponding entry made to the schedule. When you press OK and SDS2 piecemarking evaluates your change, a new Piecemark may be assigned.
End operation: None or Hook or Bend.
None specifies a DBA that is straight (not deformed).
Hook specifies a hooked DBA that is modeled based on the Hook type that is specified below.
Bend specifies a bent DBA with a bend that begins at the Distance to bend. The angle of the bend is the Bend angle.
If End operation
is locked, you can make a different choice that no longer matches the corresponding entry made to the schedule. When you press OK and SDS2 piecemarking evaluates your change, a new Piecemark may be assigned.
Hook type: 180 or 90 or - 90 or -180.
If End operation
is locked, you can make a different choice that no longer matches the corresponding entry made to the schedule. When you press OK and SDS2 piecemarking evaluates your change, a new Piecemark may be assigned.
Distance to bend: The distance from the surface of the embed to the bend.
If Distance to bend
is locked, you can select a different distance that no longer matches the corresponding entry made to the schedule. When you press OK and SDS2 piecemarking evaluates your change, a new Piecemark may be assigned.
Bend angle: A positive or negative number of degrees. A negative sign (-) sets the direction of the bend to be opposite to an equivalent entry with no negative sign.
If Bend angle
is locked, you can select a different angle that no longer matches the corresponding entry made to the schedule. When you press OK and SDS2 piecemarking evaluates your change, a new Piecemark may be assigned.
Pattern
Rotation: A positive or negative (-) number of degrees from -180 to 180. Each of the DBAs in the pattern are rotated by this amount.
If Rotation
is locked, you can enter a different angle that no longer matches the corresponding entry made to the schedule. When you press OK and SDS2 piecemarking evaluates your change, a new Piecemark may be assigned.
Rows: The number of rows of deformed bars. A single distance or variable spacing can be entered as the Row spacing for these rows.
![]()
3 is the number of deformed bar rows in this example. If Rows
is locked, you can type a different number that no longer matches the corresponding entry made to the schedule. When you press OK and SDS2 piecemarking evaluates your change, a new Piecemark may be assigned.
Columns: The number of columns of deformed bars.
![]()
3 is the number of deformed bar columns in this example. If Columns
is locked, you can type a different number that no longer matches the corresponding entry made to the schedule. When you press OK and SDS2 piecemarking evaluates your change, a new Piecemark may be assigned.
Row spacing: A center-to-center distance between adjacent Rows of deformed bars. This distance is measured vertically in the typical situation where the embed plate's Left elevation and Right elevation are the same.
![]()
rsp = row spacing. Row spacing ( variable ) can be entered as the examples in the following table show. The left-to-right spacing that you enter here equates to top-to-bottom DBA row spacing on the actual embed plate.
Variable Deformed Bar Row Spacing Rows Spacing Result 5 3,5,3,3 4 spaces at 3", 5", 3" and 3" 5 3,5,2@3 4 spaces at 3", 5", 3" and 3" 5 3,5,3 4 spaces at 3", 5", 3" and 3"
(Three spacings are entered, but four are required since the number of rows is 5. The last value is repeated to fill the fourth space.)If Row spacing
is locked, you can type a different spacing that no longer matches the corresponding entry made to the schedule. When you press OK and SDS2 piecemarking evaluates your change, a new Piecemark may be assigned.
Column spacing: The distance between adjacent columns of deformed bars. Column spacing is a horizontal dimension. Deformed bar columns run vertically, and the spacing between them is measured horizontally.
![]()
csp = column spacing. If Column spacing
is locked, you can type a different spacing that no longer matches the corresponding entry made to the schedule. When you press OK and SDS2 piecemarking evaluates your change, a new Piecemark may be assigned.
Vertical edge distance: The distance from the top edge of the embed plate to the first row of deformed bars.
![]()
ved = vertical edge distance. If Vertical edge distance
is locked, you can type a different distance that no longer matches the corresponding entry made to the schedule. When you press OK and SDS2 piecemarking evaluates your change, a new Piecemark may be assigned.
Horizontal pattern offset: A distance that the DBA pattern is offset. To change the entry made here, Horizontal pattern offset needs to be locked.
0 centers the deformed bar pattern at the horizontal center of the embed plate, half way between the plate's vertical edges.
A positive distance offsets the center of the deformed bar pattern that distance away from the true horizontal center of the embed plate. The pattern is moved away from the origin point.
A negative distance does the opposite of entering a positive offset. The pattern is moved toward the origin point..
If Horizontal pattern offset
is locked, you can type a different distance that no longer matches the corresponding entry made to the schedule. When you press OK and SDS2 piecemarking evaluates your change, a new Piecemark may be assigned.
Stud Pattern
Stud grade: A108 or A493 or etc.
If Stud grade
is locked, you can enter a different grade. That new grade will no longer match the corresponding entry made to the schedule. When you press OK and SDS2 piecemarking evaluates your change, a new Piecemark may be assigned.
Setup: If the grade of steel you want is not shown in the
list box, you can use Home > Project Settings > Job > Material Grades > Shear and Threaded Stud Grades to add it to this list.
Stud dimensions
Length: The distance between the two ends of the embed shear studs. The head is included in the length of a shear stud.
l = length ![]()
If stud Length
is locked, you can enter a different length. That new length will no longer match the corresponding entry made to the schedule. When you press OK and SDS2 piecemarking evaluates your change, a new Piecemark may be assigned.
Diameter: The diameter of the shafts of the embed plate shear studs.
![]()
d = diameter If stud Length
is locked, you can enter a different diameter. That new diameter will no longer match the corresponding entry made to the schedule. When you press OK and SDS2 piecemarking evaluates your change, a new Piecemark may be assigned.
Warning: Do not change the Stud diameter of embed plate shear studs on the Shear or Threaded Stud Material window -- change their Stud diameter here instead. See this warning for an explanation of why.
Stud head dimensions
Thickness: The distance between the top of the head and the lower edge of the head. Enter a stud head Length of 0 to get shear studs without heads.
ht = head thickness ![]()
If stud head Thickness
is locked, you can enter a different thickness. That new thickness will no longer match the corresponding entry made to the schedule. When you press OK and SDS2 piecemarking evaluates your change, a new Piecemark may be assigned.
Diameter: The diameter of the shear stud's head. Making this the same as the stud Diameter results in shear studs without heads.
![]()
hd = head diameter If stud head Diameter
is locked, you can enter a different diameter. That new diameter will no longer match the corresponding entry made to the schedule. When you press OK and SDS2 piecemarkng evaluates your change, a new Piecemark may be assigned.
Pattern
Rows: The number of rows of studs.
![]()
3 is the number of stud rows in this example. If stud Rows
is locked, you can enter a different number. That new count will no longer match the corresponding entry made to the schedule. When you press OK and SDS2 piecemarking evaluates your change, a new Piecemark may be assigned.
Columns: The number of columns of studs.
![]()
3 is the number of stud columns in this example. If stud Columns
is locked, you can enter a different number. That new count will no longer match the corresponding entry made to the schedule. When you press OK and SDS2 piecemarking evaluates your change, a new Piecemark may be assigned.
Row spacing: A center-to-center distance between adjacent Rows of studs. This distance is measured vertically in the typical situation where the embed plate's Left elevation and Right elevation are the same.
![]()
rsp = row spacing. Row spacing ( variable ) can be entered in a number of different ways, as the examples in the following table show. The left-to-right spacing that you enter here equates to top-to-bottom stud row spacing on the actual embed plate.
Variable Stud Row Spacing Rows Spacing Result 5 3,5,3,3 4 spaces at 3", 5", 3" and 3" 5 3,5,2@3 4 spaces at 3", 5", 3" and 3" 5 3,5,3 4 spaces at 3", 5", 3" and 3"
(Three spacings are entered, but four are required since the number of rows is 5. The last value is repeated to fill the fourth space.)If stud pattern Row spacing
is locked, you can enter a different distance. That new row spacing will no longer match the corresponding entry made to the schedule. When you press OK and SDS2 piecemarking evaluates your change, a new Piecemark may be assigned.
Column spacing: The distance between adjacent columns of studs.
![]()
csp = column spacing. If the stud pattern Column spacing
is locked, you can enter a different distance. That new column spacing will no longer match the corresponding entry made to the schedule. When you press OK and SDS2 piecemarking evaluates your change, a new Piecemark may be assigned.
Vertical edge distance: The distance from the top edge of the embed plate to the first row of shear studs.
![]()
ved = vertical edge distance. If the stud pattern Vertical edge distance
is locked, you can enter a different distance. That new vertical edge distance will no longer match the corresponding entry made to the schedule. When you press OK and SDS2 piecemarking evaluates your change, a new Piecemark may be assigned.
Horizontal pattern offset: A distance that the stud pattern is offset. To change the entry made here, Horizontal pattern offset needs to be locked.
0 centers the stud pattern at the horizontal center of the embed plate, half way between the plate's vertical edges.
A positive distance offsets the center of the stud pattern that distance away from the true horizontal center of the embed plate. The stud pattern is moved away from the origin point.
A negative distance does the opposite of entering a positive offset. The stud pattern is moved toward the origin point.
Copy, Paste, Save, Load buttons:
Properties opens the Edit Properties window, on which you can make entries to custom properties. If your current Job was set to use a legacy flavor when it was created, the window that opens is named Custom Properties, not Edit Properties.
Tip: The Edit Properties window can also be used to read
Log entries or review or type
Notes.
Tip: The Member Properties command is an alternative to this button. It opens the Edit Properties window directly, without your first having to open a member edit window.
Status opens the Member Status Review window, which can give you additional information about the member, and which you can use to enter status information or designate a member as an existing member.
Note: This button shows
if one or more Repeat check boxes on the Member Status Review window do not match the checked-unchecked state of same-named fields in User and Site Options > Site > Member status items to copy/repeat. On the Status Review window, the fields that do not match User and Site Options are plotted in red.
OK (or the Enter key) closes the edit window and saves any changes you have made on the window to the member file.
Solids on OK : If the appropriate choice is made to User and Site Options > Modeling > Automatically process after modeling operation, then this member will automatically be regenerated (Create Solids will take place) after your press OK. Otherwise, you will have to manually Process and Create Solids in order for changes you made on this window to be fully updated in the 3D model.
Change all: If you Edit Member (one member only) and make a change that potentially triggers the "Do you want to change all" dialog and the 3D model contains more than one member of the same type that has the same piecemark as the member you changed, a yes-no dialog opens. On it is the question, "Do you want to change all (members with this piecemark)." Press the Yes button to change all the members; press the No button to change only this member.
Cancel (or the Esc key or the button) closes the edit window without saving any changes that you have made.
Tip: Any time you use Edit Member just to review a member (and you do not want to set the defaults for to-be-added members), the best way to close this window is to Cancel.
By supporting member's end
1. Click the Embed Plate icon, which is pictured above. The icon can be found on the Members page > Embed section.
Alternative: Invoke Embed Plate using the Find Tool by searching the command name and clicking the icon, which is pictured above.
Learn more about alternative methods for launching commands.
2.The Select add method window opens. Select by supporting member's end and press OK.
3. The status line prompts, Select supporting beam(s) and/or joist(s). Select the beam(s) or joist(s) and press enter or right-click (OK).
Alternative: Right-click (Return) or press the Esc button to end the operation.
4. The status line prompts, Select end(s) on member. Select the left end, right end, or both ends and press enter or right-click (OK).
Alternative: Right-click (Return) or press the Esc button to end the operation.
5. The Embed Plate Edit window opens. After you are done changing or reviewing settings, left-click on the OK button to finish adding the embed members to the selected end(s).
Alternative: Left-click the Cancel button to stop the embed member from being added to the model.
By selecting end-points or mid-point
1. Click the Embed Plate icon, which is pictured above. The icon can be found on the Members page > Embed section.
Alternative: Invoke Embed Plate using the Find Tool by searching the command name and clicking the icon, which is pictured above.
Learn more about alternative methods for launching commands.
2.The Select add method window opens. Select by selecting end-points or mid-point and press OK.
3. The status line prompts, Embed Plate: Locate top-left corner or mid-point. Various Locate options become active along with Locate - Repeat - Return mouse bindings.
Select the Locate icon you want. Place the point location target where you want the first work point of the embed, then left-click (Locate).
Alternative: Right-click (Return) or press the Esc button to end the operation.
4. The status line prompts, Embed Plate: Locate top-left corner or mid-point. Place the point location target where you want the second work point of the embed, then left-click (Locate). This sets the length of the embed.
Alternative: Right-click (Return) to set the first selected point as the midpoint of the embed.
5. The Embed Plate Edit window opens. After you are done changing or reviewing settings, left-click on the OK button to finish adding the embed member.
Alternative: Left-click the Cancel button to stop the embed member from being added to the model.
- Custom members
- Embed Schedule
- Embed
- Embed Layout Add Tool
- Shear connection to an embed in a concrete wall
- Clip angle to an embed in a concrete wall
- Beam seat to an embed in a concrete wall
- Beam to concrete bearing connections
- Joist top chord to concrete with pocket & bearing embed
- Top chord joist seat to an embed
- Extended joist bottom chord stabilizer to an embed